Plastic Injection Molding vs. 3D Printing: Which is Right for Your Product?
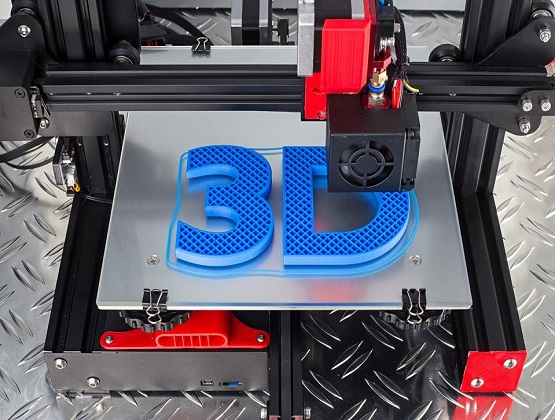
hen it comes to manufacturing, choosing a suitable method can impact everything from cost to product quality and production speed. Two popular methods—plastic injection molding and 3D printing—each have unique advantages suited to different needs. Here, we’ll explore how each technique works and its strengths, limitations, applications, and costs to help you select the best manufacturing process for your product.
What is Plastic Injection Molding?
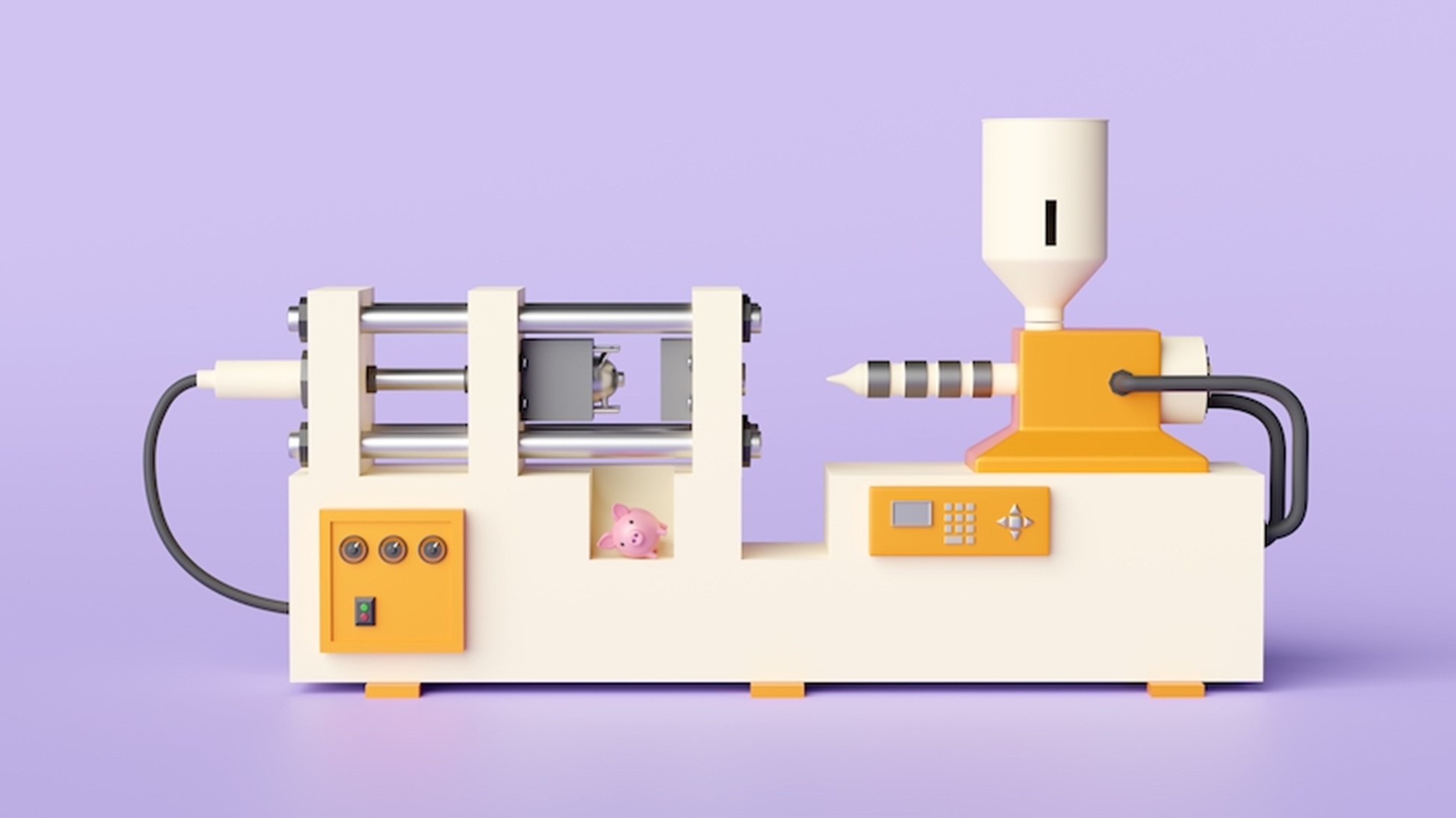
Plastic injection molding is when molten plastic is injected into a pre-designed mold, cooled, and ejected as a solid part. This technique, widely used in the automotive and consumer goods industries, quickly and efficiently produces high volumes of consistent parts. According to Essentra Components, injection molding is excellent for creating complex parts with consistent dimensions and quality, making it suitable for durable, high-volume production.
How Does Injection Molding Work?
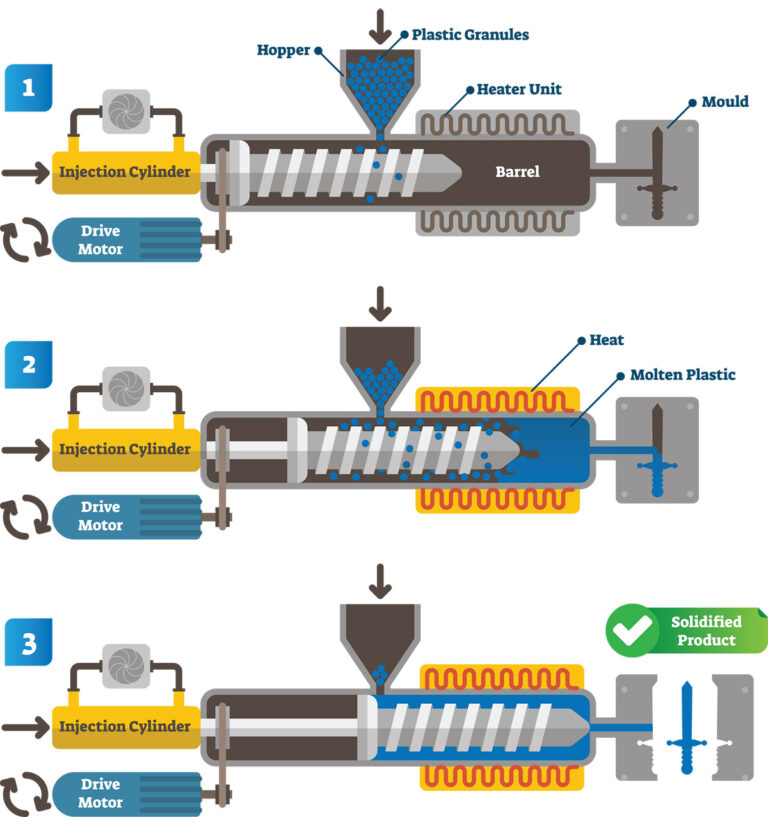
- Mold Creation: A custom mold, typically made from metal, is designed and crafted to match the final product’s shape and specifications.
- Clamping: The mold is placed in an injection molding machine and clamped securely to prepare for the injection process.
- Injection: Molten plastic pellets are heated and injected into the mold cavity under high pressure, ensuring the molten material fills all areas of the mold.
- Cooling: The plastic cools and solidifies within the mold, taking its shape.
- Ejection: Once cooled, the mold opens, and the part is ejected using an ejector mechanism.
- Trimming and Finishing: Any excess material (known as flash) is trimmed away, and the part is polished if needed to ensure a clean finish.
This efficient, streamlined process allows for high-speed production of durable, consistent parts, making injection molding ideal for large-scale manufacturing.
Applications for Plastic Injection Molding
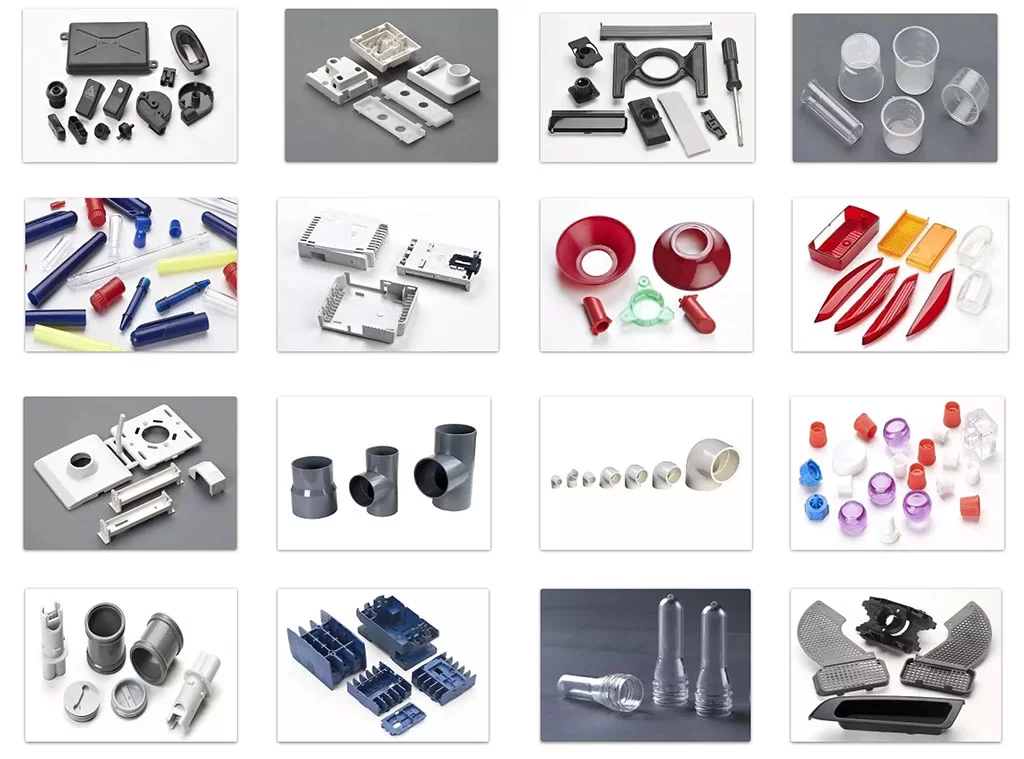
- Automotive Components: Commonly used for dashboard panels, handles, and buttons that require precision and durability.
- Consumer Electronics: Used for producing high-quality casings, such as those for smartphones and remote controls.
- Medical Devices: Creating sterile, consistent parts like syringes and IV components is essential.
- Household Goods: Ideal for mass-producing items like containers, cutlery, and furniture parts.
- Packaging: Frequently used for caps, closures, and durable plastic containers, which benefit from high-speed, uniform production.
Pros of Plastic Injection Molding
- Cost-Effective for High Volumes: Once the initial tooling is complete, injection molding offers low per-unit costs for large production runs.
- Durability and Consistency: The process produces durable parts with smooth finishes and minimal defects.
- Fast Production: Thousands of parts can be produced daily, meeting high demand efficiently.
Cost of Plastic Injection Molding
- Initial Tooling Costs: Creating custom molds can cost between $5,000 and $100,000 or more, depending on the mold's complexity and material. This high upfront cost makes injection molding more suitable for high-volume production.
- Per-Unit Cost: Once the mold is created, the per-unit cost decreases significantly as volume increases, often ranging from $0.10 to $2 per part in large production runs. This scalability makes injection molding cost-effective for mass production but less practical for small-batch or custom orders.
What is 3D Printing?
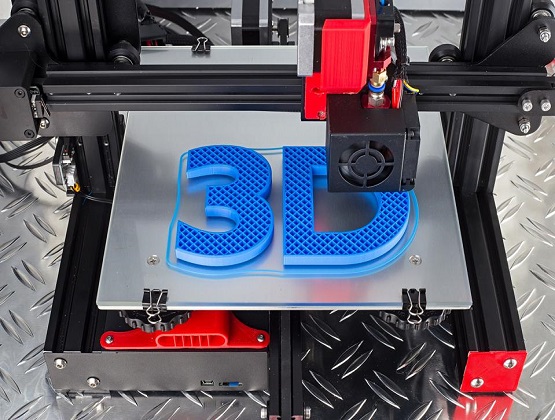
3D printing, or additive manufacturing, builds objects layer by layer from a digital model. Unlike injection molding, 3D printing doesn’t require molding, allowing for faster prototyping and a flexible design process. 3D printing is trendy for creating prototypes, custom parts, and small production runs. This technology supports intricate designs and can work with various materials, from plastics to metals.
How Does 3D Printing Work?
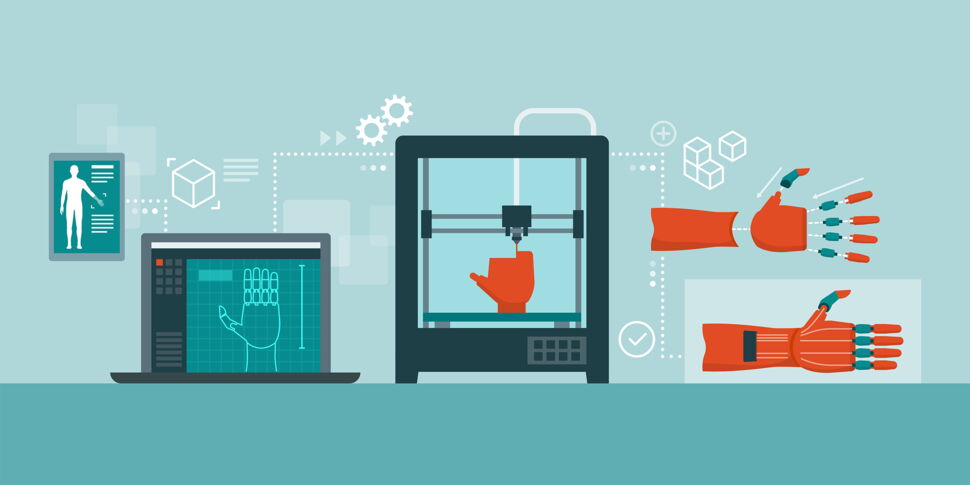
- Design Creation: A digital 3D model is created using computer-aided design (CAD) software.
- Slicing: The 3D model is divided into thin, horizontal layers, creating a “blueprint” for the printer.
- Printing: The printer builds the part layer by layer, using materials such as plastic, resin, or metal. Each layer is precisely placed according to the digital model.
- Cooling or Curing: Depending on the material and 3D printing method, each layer cools or undergoes curing (solidifying) to form a cohesive structure.
- Post-Processing: The printed part may undergo additional steps like polishing, cleaning, or curing to achieve the desired finish and quality.
This flexible, layer-by-layer approach is ideal for prototyping, small-batch production, and creating intricate shapes that are difficult to achieve with other methods.
Applications for 3D Printing
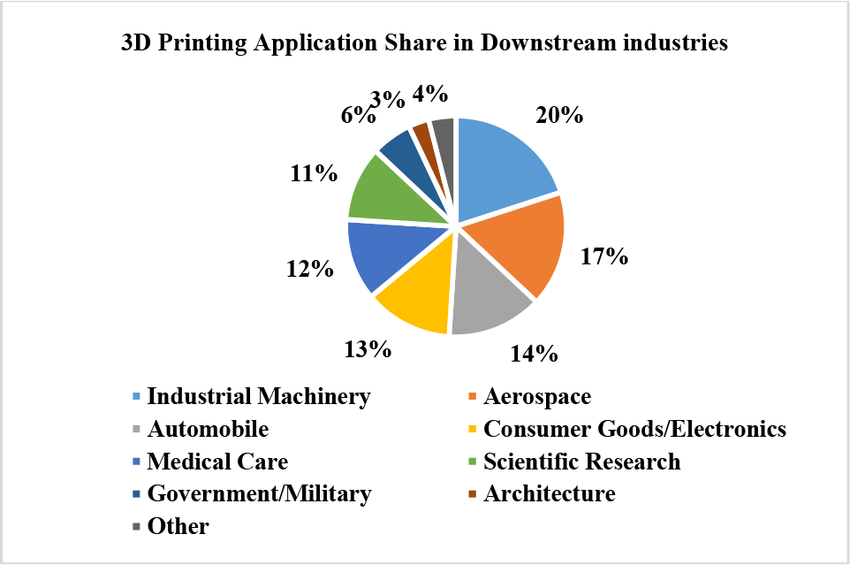
- Prototyping and Product Development: Enables fast, cost-effective testing and refinement of designs.
- Medical and Dental Applications: Used to create custom implants, prosthetics, knee braces, and dental aligners tailored to individual needs.
- Consumer Goods Products: Usually consist of customized and unique parts for a particular consumer group that cares more about personalized products, such as decorations, toy parts, containers, and cases.
- Aerospace Components: Ideal for producing lightweight, complex parts, such as brackets and engine components. They are mainly made through metal printing.
- Jewelry and Fashion: Allows for unique, intricate designs that are difficult to achieve through traditional methods.
- Architectural Models: Used by architects to create detailed building models for client presentations.
Types of 3D Printing
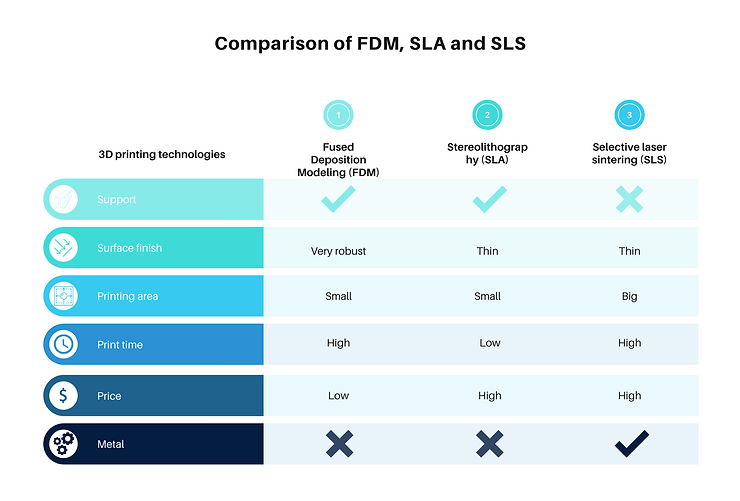
Various types of 3D printing, including Fused Deposition Modeling (FDM), Stereolithography (SLA), and Selective Laser Sintering (SLS), offer different material options, detail levels, and durability. FDM is commonly used for functional prototypes and end-use parts due to its affordability and versatility. For instance, Formlabs provides high-precision printers, particularly SLA models, that serve industries like medical devices and engineering, where accuracy and material properties are crucial.
Pros of 3D Printing
- Rapid Prototyping and Design Flexibility: Enables fast adjustments without costly molds.
- No Upfront Tooling Cost: Cost-effective for low-volume production and custom parts.
- Complex Geometries: These can produce intricate shapes and internal structures that are challenging to achieve with injection molding.
Cost of 3D Printing
- No Initial Tooling Cost: Unlike injection molding, 3D printing doesn’t require molds, making it more accessible for small production runs or customized products.
- Per-Unit Cost: The unit costs range from $1 to $100, depending on the material, part complexity, and 3D printing technology. This cost is competitive for low-volume production but becomes less economical than injection molding as production volume increases.
- Cost Scalability: 3D printing costs don’t decrease in volume as significantly as injection molding, making it better suited for prototyping and small-batch production.
Comparing Injection Molding and 3D Printing for Different Applications
Prototyping and Product Development
3D printing is ideal for quick, low-cost prototyping, allowing for easy refinement and testing. Injection molding, in contrast, is more suitable for large-scale production of finalized designs.
Low Volume vs. Mass Production
3D printing is practical for low-volume or custom parts due to its flexibility and minimal setup costs. For mass production, however, injection molding offers greater cost efficiency and consistent quality, with a per-unit cost that decreases as production volume increases.
Material Considerations
3D printing materials are improving, but injection molding still supports a broader range of robust plastics and composites. Injection molding is more suitable for parts requiring high strength and durability, while 3D printing excels in flexibility and customization.
When to Use 3D Printing and When to Transition to Injection Molding
For many companies, using 3D printing in the early stages and transitioning to injection molding for full-scale production provides the best of both worlds.
- Start with 3D Printing for Prototyping and Testing: 3D printing allows cost-effective design testing and refinement without molding.
- Transition to Injection Molding for Final Production: Once designs are finalized, injection molding is ideal for creating durable, high-quality parts at a lower per-unit cost for large production runs.
Conclusion: Which Manufacturing Method is Right for You?
Choosing between plastic injection molding and 3D printing depends on your product’s stage, production volume, and budget. 3D printing is well-suited for prototyping, customization, and low-volume production, while plastic injection molding is the better choice for high-volume, consistent-quality manufacturing.
By combining both methods—using 3D printing for initial development and injection molding for mass production—businesses can reduce costs, improve quality, and streamline manufacturing. This hybrid approach offers an efficient, cost-effective way to market products, balancing innovation and scalability.